How does gear reduction work?
Gear reduction is a core concept of gears that needs to be thoroughly understood in order to get the most use out of them in machines and optimize performance and efficiency.
This blog will cover gear reduction, including what it is, how it’s calculated, and common applications that rely on gear reduction to function properly.
What is gear reduction?
Gear reduction is a mechanical process used to reduce the speed and increase the torque of an input power source through a set of gears (gear train). This is achieved when one gear is driven by a smaller gear with less teeth. The gear ratio between the two gears determines the exact amount of reduction achieved.
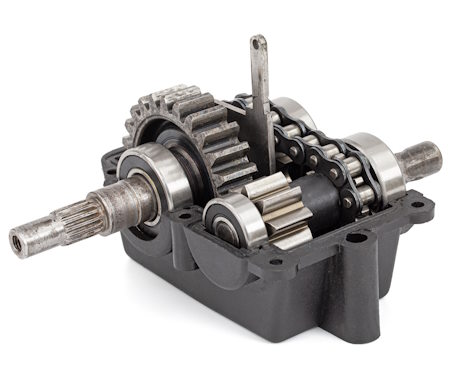
Gear reduction plays an essential role in countless applications, from heavy-duty industrial equipment to more standard devices. Having control over the speed and torque of a machine enables extremely high torque or speeds to be achieved with relative ease.
Gear ratios explained
The gear ratio of a system is the ratio of the number of teeth on the driven gear to the number of teeth on the driving gear. The formula to calculate this is below.

This ratio determines how many rotations the driving gear needs to make to turn the driven gear once. Gear ratio directly affects the speed and torque of the output shaft. A higher ratio means higher torque and lower speed, while a lower ratio means higher speed and lower torque.
For example, a gear ratio of 4:1 means the driving gear must rotate four times to rotate the driven gear once, resulting in a significant reduction in speed and increase in torque.
Related: Gear module: what is it and why is it important?
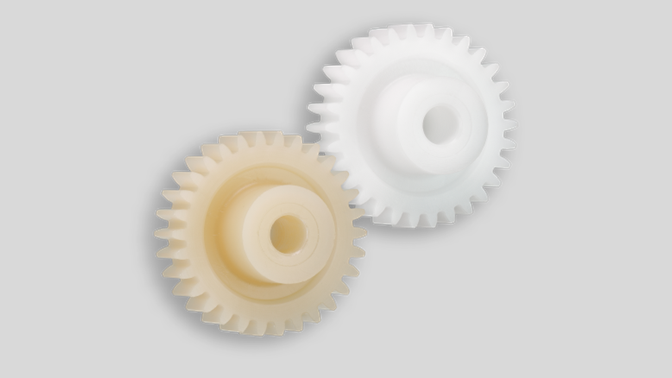
Read more: What is mechanical advantage in gears?
Inverse relationship between torque and speed
The above example highlights the inverse relationship between torque and speed. As speed decreases, torque will always increase, and vice versa. This is due to the fundamental law of conservation of energy.
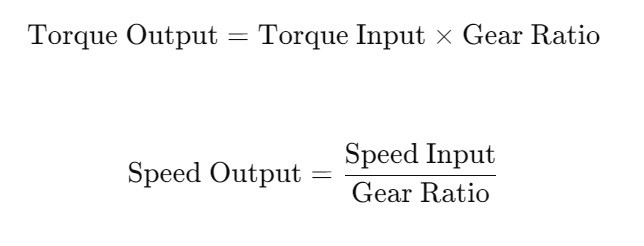
The power supplied to the system remains constant, even after gear reduction is achieved, which is why as speed decreases, torque increases by an inverse amount.
This inverse relationship is crucial in applications like automotive transmissions, where lower gears provide high levels of torque for acceleration and higher gears provide greater speed for cruising.
Efficiency factors
There are a number of different factors that impact the efficiency of gear reduction. These factors demand extensive consideration and planning to ensure a system is performing optimally.
Friction
Friction is one of the most obvious factors that can impact the efficiency of gear reduction. Higher levels of friction lead to more energy lost as heat, reducing efficiency. Adequate lubrication — while difficult to maintain and potentially harmful to the environment — can mitigate this, as well as the use of high-quality self-lubricating materials in place of metal.
Gear material
The material used for the gears also plays an important role in efficiency. Metal gears, while durable, are heavy and require more energy to move. Meanwhile, plastic gears are lighter and easier to move, but may not be able to support the same loads that metal can.

Related: Plastic gears vs. metal gears: Which is the better option?
Gear design
While spur gears are the most popular type of gear, they are not the most efficient. Other gear designs, like helical gears, are more efficient when transferring energy. This is due to the slanted tooth angle of helical gears, which enables smoother meshing.
Other design factors like surface finish or axis configuration can also impact the efficiency of gear reduction systems.
Alignment and mounting
Poor alignment and mounting often leads to increased friction and wear, reducing efficiency. A high level of precision in installation and maintenance is crucial to achieve optimal performance.
Load conditions
Different gears are designed to handle different loads, and a gear will only achieve peak efficiency if it’s operating under the ideal load conditions. Deviations from this ideal range can result in significant losses to efficiency.
Temperature
High operating temperatures can affect the viscosity of lubricating grease — if it’s being used — and the expansion of gear materials, impacting efficiency. Effective cooling and temperature control mechanisms are vital to keeping operating temperature within the ideal range.
Common applications of gear reduction
Automotive industry
Gear reduction is essential in vehicle transmissions, as previously mentioned. As a vehicle shifts up, less torque is needed in favor of more speed, which is best achieved through gear reduction.
Industrial machinery
Heavy-duty machinery such as conveyor belts and cranes are frequently moving heavy loads at relatively low speeds, which requires significant torque. Gear reduction allows the necessary torque to be achieved in these applications.
Household appliances
Even household appliances like washing machines or blenders make use of gear reduction. Both of these devices utilize high-speed motors that need to be balanced out through gear reduction to achieve lower speed, higher torque operation.
Automation and robotics
Gear reduction enables highly precise movements in robotic arms and other automated systems. Given the high levels of precision required in these applications, the use of gear reduction is essential.
Recap
Understanding gear reduction is essential for optimizing the performance and efficiency of machines across a wide range of applications. From the automotive industry to household appliances and robotics, gear reduction plays a critical role in managing the relationship between speed and torque to meet specific operational needs. By carefully considering factors like gear ratio, material selection, design, and environmental conditions, engineers can maximize the effectiveness of gear reduction systems.